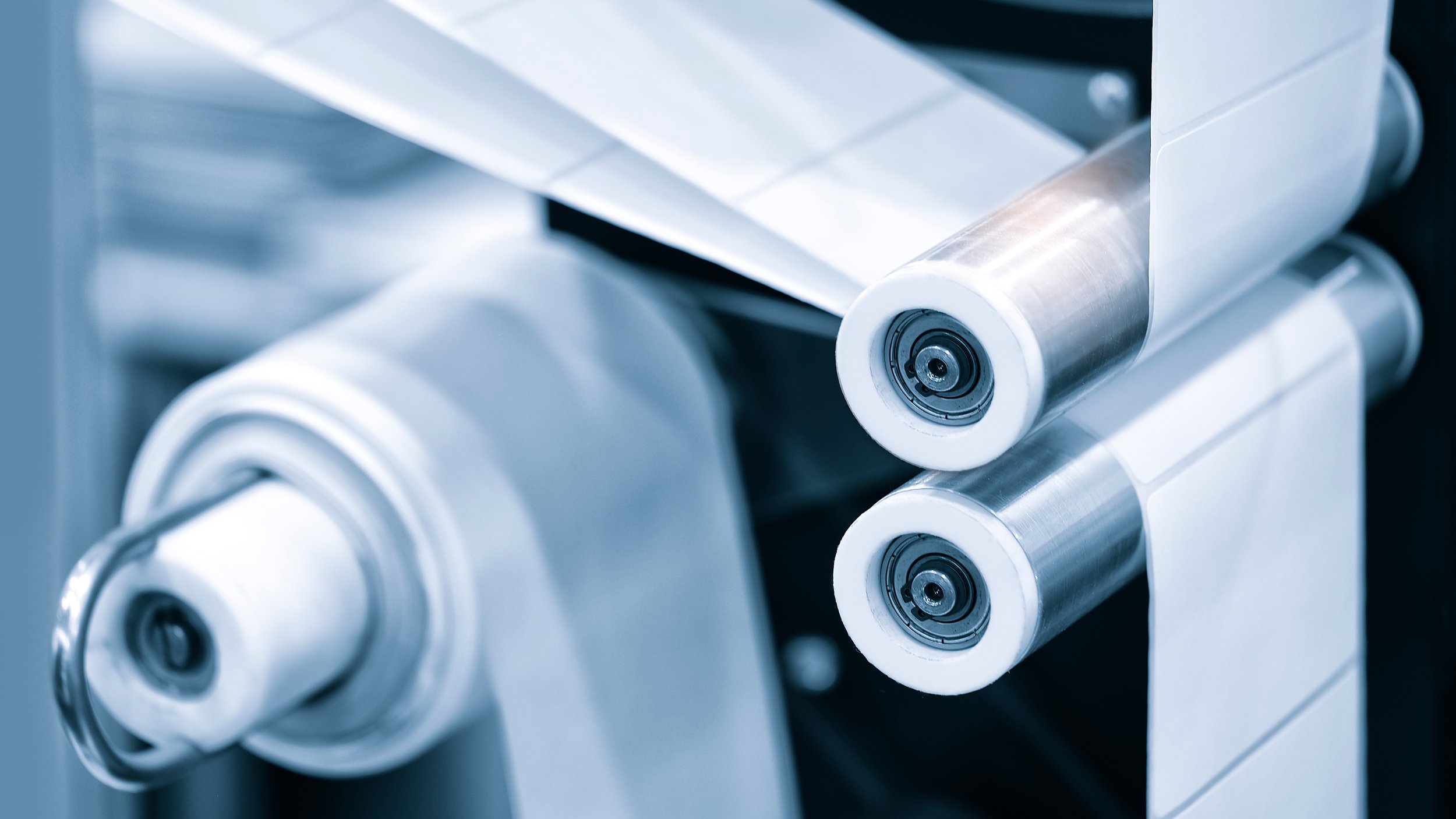
Labels
Labeling with Purpose.
Clarity, Compliance, and Creativity.
What You Need to Know About Labels
Pressure-sensitive labels, often referred to as self-adhesive labels, are used across industries for their ease of application and adaptability. This section will introduce you to the basics of pressure-sensitive labels and the critical information you need to make informed packaging decisions, ensuring product protection, compliance, and user-friendly designs.
Anatomy of a
Label Roll
Face Stock: The printed material seen by customers, commonly paper or film.
Adhesive: The sticky layer that allows the label to adhere to the product. Available in permanent, removable, and all-temperature options.
Liner: The backing or carrier that allows easy removal of the label. Typically made of kraft paper or PET for increased sustainability and productivity.
Top Coating: A protective layer that can be either visible (e.g., gloss or matte) or invisible to protect the face stock.
Core: The sturdy center of the label roll, typically made of cardboard, with standard sizes of 1 inch or 3 inches depending on the label application equipment.
Choosing the Right Label Type
There are two primary types of pressure-sensitive labels: single-ply and multi-ply. Single-ply labels are used for standard product information, while multi-ply labels are ideal for extended content and regulatory information. Multi-ply labels can accommodate more information without increasing the overall size of the package, ensuring compliance with various industry regulations.
Learn more about multi-ply labels in the
Extended Content section.
Critical Labeling Considerations
Choosing the right label involves multiple factors, from the container surface to environmental exposure.
Each consideration helps ensure optimal performance and durability.
-
The shape, material, and texture of the container (e.g., flat, curved, rigid, squeezable) affect label adhesion and appearance. Smooth surfaces generally ensure better adhesion, while textured or flexible surfaces may require specific adhesives or label materials to ensure a secure fit. For example, a small-diameter, curved surface might need a thinner, more flexible label.
-
Whether labels are applied by hand or machine affects the speed and precision of the process. Machine-applied labels require careful consideration of application speed, temperature, and environment, while hand-applied labels might allow for more flexibility but may increase the risk of misalignment. Ensure that the label and adhesive are compatible with the application method.
-
Consider the conditions the label will face throughout its lifecycle, such as exposure to moisture, extreme temperatures, UV light, or chemicals. Labels exposed to outdoor elements, high humidity, or refrigeration need to withstand these environments without losing adhesion or legibility. Specific adhesives and coatings like UV-resistant or water-resistant options should be selected accordingly.
-
Different face stock materials (e.g., paper or film) and adhesives (e.g., permanent, removable, all-temperature) affect label performance. The stock must suit the product’s needs, such as flexibility for squeezable containers or durability for products exposed to heat. The adhesive must match the container’s material and surface treatment for optimal adhesion, be it for permanent or removable applications.
-
Proper storage of label rolls is essential for maintaining quality, especially in controlled environments like clean rooms or warehouses. Consider the recommended storage conditions such as temperature and humidity to ensure labels do not lose their adhesive properties or become damaged before use. The service conditions, such as exposure to chemicals or outdoor elements, will dictate the label’s durability.
-
The core size (typically 1 inch or 3 inches) must match the labeling equipment for efficient application. Roll dimensions, including the maximum outer diameter and the number of labels per roll, are important for ensuring compatibility with your production line and minimizing downtime due to roll changes.
Enhancing Labels with Specialty Features
In addition to standard label components, pressure-sensitive labels can include specialty finishes like embossing, foil stamping, laminating, and silk screening. These finishes enhance both the visual appeal and functionality of the label, making it stand out on the shelf and adding durability.
Printing Technologies for Pressure-Sensitive Labels
Pressure-sensitive labels are typically printed using flexographic presses, which offer flexibility in ink and coating options. Flexo presses can print up to 10 ink stations for single-ply labels and up to 9 stations for multi-ply labels. When designing for flexo printing, it’s essential to follow specific guidelines, such as ensuring minimum dot size, barcode dimensions, and proper line thickness.
Ready to Choose the Right Label?
Explore our extensive range of pressure-sensitive labels and get started on selecting the best options for your product. Whether you need single-ply or multi-ply labels, our team is ready to help you meet your labeling needs.
Keep exploring
Structure
Design
Labels
Sustainability
Extended Content